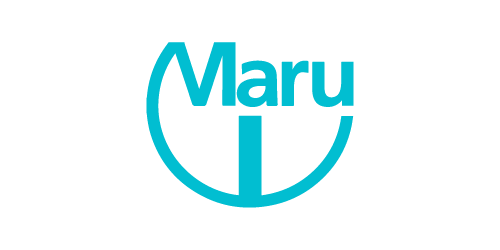
会社名 | 株式会社丸山製作所 |
---|---|
事業内容 | 金属切削加工部品の製造 |
創業 | 昭和33年11月 |
従業員数 | 125名 (2025年1月現在) |
URL | https://egaoseizou.co.jp/ |
概要
創業60年を超え、複数拠点を抱える株式会社 丸山製作所様。生産性15%向上を目指してMESを中心としたシステム構築のサポートをしております。今回、第9回 スマート工場EXPOのセミナーで導入事例として紹介するにあたり、株式会社 丸山製作所(以下、丸山製作所)様にインタビューさせていただいた内容をご紹介いたします。
事例詳細
導入背景
「工程間の壁をなくす」をキーワードに、知識と経験に頼らない、誰でも簡単に確認実行できる「仕組み」づくりを構築し、生産性15%向上を目指す丸山製作所様。創業60年を超える、金属の切削加工と組立作業を得意としている企業です。
製造現場にはまだ人に頼る部分が多くあり、限られた人材の中で事業を拡大させていくには運用体制の見直しや負荷の高い工程への設備投資、人作業の自動化、生産手順などの固定概念の見直しを迫られていました。
現状と課題
自動化設備への投資や固定概念(既存のルール)を見直して生産の最適化をはかるには、まず現状を正確に把握することが求められます。丸山製作所様ではまず最初に、現状の把握の手段、設備導入などの根拠になるデータを取得するためにも、誰でも簡単に生産状況が確認できる仕組みづくり、環境の整備に着手しました。
豊富な知識を有した熟練者でないと生産計画が立てられず、必要な知識量が多岐にわたるため教育コストが高い
課題2:進捗確認の困難さ各工程のリアルタイムな進捗確認は現場に直接行かなければならない
課題3:作業負荷の大きい出荷製品管理生産計画をもとにホワイトボードに紙の予定表を掲示して、出荷したら剥がすというような出荷製品管理を行っていたため、管理者と作業者の両方に作業負荷が大きい
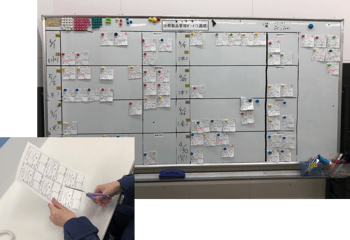
ホワイトボードによる出荷管理
導入後の成果
計画作業の属人化排除
丸山製作所様では、まず生産スケジューラーの導入を支援させていただきました。(Y's-SF Scheduler)
生産スケジューラーはマスター整備が一番の肝です。熟練者の頭の中にしかない経験やノウハウを定量化・数式化することで属人化の排除や再計画時の計画時間短縮、作業負荷の均一化をすることができました。
MES(製造実行管理システム / Y's-SF Premium)の導入では、設備の稼働状況や生産実績を収集し、事務所や工場内からWEB上で確認できる状態にしました。設備異常がすぐにわかる設備稼働状況MAPは工程担当者以外でも監視・フォローができ、迅速に復帰対応することで設備停止時間が約3%短縮されました。また、計画達成度の確認により、遅れている工程への迅速な応援指示で納期の順守率が向上しました。
本社以外の工場の生産状況についても、Y's-SF Premiumの複数工場連携機能により、本社工場からモニター上でいつでも確認できるようになっています。
スケジューラーとMESの両方を導入したことにより計画と実績がデータ化され、これまで紙ベースで行っていた出荷製品管理も遠隔地からモニター上でリアルタイムに把握することが可能になりました。
今まで紙で管理していたものが自動で行われるようになったため、管理にかかる時間は98%程度の削減になっています。また、紙などを使用せず、モニター上で確認可能なため資源の削減にもつながっています。
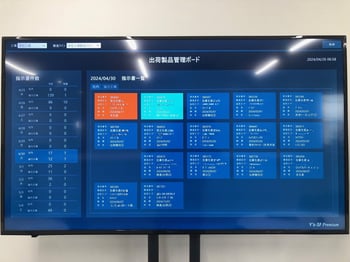
デジタル化されたホワイトボードタッチモニターで直感的に操作可能
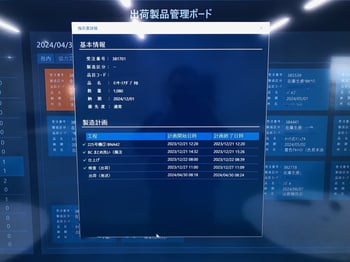
カードをタップすることで詳細を表示
今後の取り組み
丸山製作所様では、今後の取り組みとして、負荷の高い工程への自動化設備の導入や生産手順などの固定概念の見直しを図り、生産性15%向上を目指して改善を進めていく予定です。
セミナー動画
インタビュー
スケジューラーの導入にあたって
スケジューラーの導入で一番苦労された点はどういったところでしょうか
まず、スケジューラーを導入する前はどの設備がどの製品を加工できるのか、特定の担当者でないとわからない状況がありましたので、その担当者の頭のなかにあるものをアウトプットすることが一番時間もかかり苦労しました。
製造業というのはそこが一番課題で、頭の中にあるものを出すというのが一番大変です。
どの設備がどの製品を加工できるのかわからないというお話がありましたが、どの設備を組み合わせて製品を作るか、という決定は人に依存していた部分があったということでしょうか
私たちの会社の設備は同じ設備でもスペックが微妙に違います。設備導入時にスペックを決めて導入していますので同じ機械のように見えても別の機械のようなものです。生産計画は専門の部署で立てますが、設備に関しての知識はありません。そうすると設備導入を担当した人でないとわからないという状態がありました。設備のスペックや生産計画のこともわかる、工場全体を見えている人だからこそ出来ている部分というのがあったので他の人がやるというのは難しい部分がありました。スケジューラーの導入にあたっては、その部分を数値化するなどしてマスター整備する必要があり、大変苦労しましたが、マスター調整を繰り返すことで徐々に思った通りの計画が立てられるようになりつつあります。
アナログな出荷製品管理からの脱却
システムを入れる前は出荷製品管理をホワイトボードで行っていたそうですが、管理するうえで困っていた点はありますか
私たちの会社の管理部門は2階に位置しており、1階の製造現場まで納入予定日票を印刷して持っていき、ホワイトボードに掲示するという作業が発生していました。納入予定日票は紙なので紛失してしまったり、計画変更で貼り換えが必要な場合に対象の予定日票を探すのに時間がかかっていました。また、前の予定日票が残ったままになっていてどちらが最新かわからなくなることや、人によって掲示の仕方に独自ルールがあることなど、様々な問題点がありました。スケジューラーが導入される前は現場作業員が作業の順番を決定していたのですが、現場担当者は全体を把握しているわけではないので「納期に間に合えばいいだろう」という考えで順番を決めてしまっている部分もありました。
ホワイトボードがデジタル化されて、どのような効果があったか教えてください
納入予定日票のデータ作成や掲示作業をしなくてよくなったのは大きいですね。人作業による管理はどうしてもどこかでミスが発生することがありますが、スケジューラーで立てた計画から予定日票のカードを自動生成し、MESの実績収集機能で製品の現在位置を取得するので管理コストは大幅に削減できたと思います。紙で管理をしなくなったので、副次的にCo2などの資源削減効果も得ることができました。ホワイトボードでは、どうしても掲示できる情報が限られるため、予定日票に記載する項目を最小限に絞っても、だいたい一週間程度の予定しか掲示することができませんでした。しかし、予定日票がデジタル化されたことで、もっと先の予定も視覚的に見えるようになり、仕掛品の把握もしやすくなっています。
今回、システム導入することで注文単位ごとに製品の現在位置を表示することが可能になりました
ホワイトボードでの管理の場合、製品の現在位置の確認というのはどのようにされていましたか
リアルタイムな製品の位置や進捗などは現場に行って確認していましたね。システム導入後はどこにいてもネットワーク上で現在位置や計画に対する進捗が見れるようになったので、出荷予定に対しての遅れなどが確認しやすくなり、納期の順守率アップにもつながっています。
数字で測れない、人への導入効果
属人化の排除や生産性の向上、Co2の削減効果など様々な導入効果を挙げていただきましたが、他に印象的な導入効果がありましたら教えてください
人の作業というのは設備と違って作業の着手完了の記録が正確にとれるものではないため、計画上の誤差がどうしても多く発生してしまいます。そのため計画上ゆとりのある場合などは「ゆっくり作業しよう」ですとか「仕事がなくなってくると不安だから少し仕事をためておこう」といった、現場による時間調整のようなものが発生していました。スケジューラーの導入にあたり、そういった人作業の時間も数値化することで、ゆとりのある工程がわかるようになりました。また、MESの実績収集・見える化機能により現在どこの工程が忙しいのかなどが見えるようになり、ゆとりのある工程から人員を適切に配置することで生産能力のアップにつながっています。元々「工程間の壁をなくそう」という思いで導入しました。そういった意味で、現場作業員の「自工程の仕事量が少ないことによる不安」を他工程への応援で解消し、より意欲的に仕事に取り組んでもらえるようになりました。
システムの導入を通して現場の雰囲気の変化などはありましたか
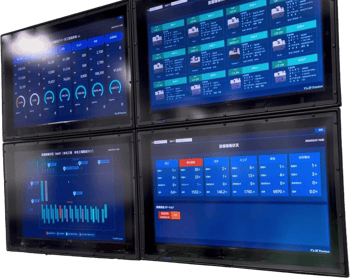
工場内に大型の見える化モニターを設置
生産状況などの画面をみんな見るようになって、現在の状況がわかるようになってきています。小集団活動の中でもMESのデータを見てリードタイムの短縮をやっていこうなど社員のほうから提案が挙がってくるようになり、意識はだいぶん変わってきていると思います。 初めに小集団活動のメンバーから「リードタイム二分の一」という目標を設定したいと提案があり、最初は無謀な目標だと言われていて、できないかもしれないと思うこともあったのですが、ダメでもやろうよという雰囲気でやっていました。
目標を設定してから、MESが入る前と後で集計を比較をしなければならないとなったときに、現状の集計ができておらず把握できていないので目標が見えない、現状がわからないので二分の一が実際どれくらいなのかわからないという問題がありました。それがMESを導入したことで「リードタイム二分の一」がより具体的な数字として見えるようになり、どこを改善するべきか明確になりました。MESを導入して、半年くらいの間に達成できるかもしれないという雰囲気になってきて、「できそうだと思えるようになってきた」と言われたときはうれしかったですね。
社員のモチベーションアップにもつながっているわけですね
そうですね。工程毎にボトルネックの部分を改善していっているのですが、当然改善していくとボトルネックというのは他の工程に移っていきます。
システムを導入して見える化することで生産性を向上させるためのボトルネックがまず見つかって、そこを改善して実績を収集することでさらにどこがボトルネックになっているか、追跡してつぶしていくことで生産性の改善が見込めています。見えるからこそ目標がきちんとできて、それに対してみんながモチベーション高くやってもらうことで、一つずつ課題をつぶして次につなげていくというサイクルができてきています。
導入製品
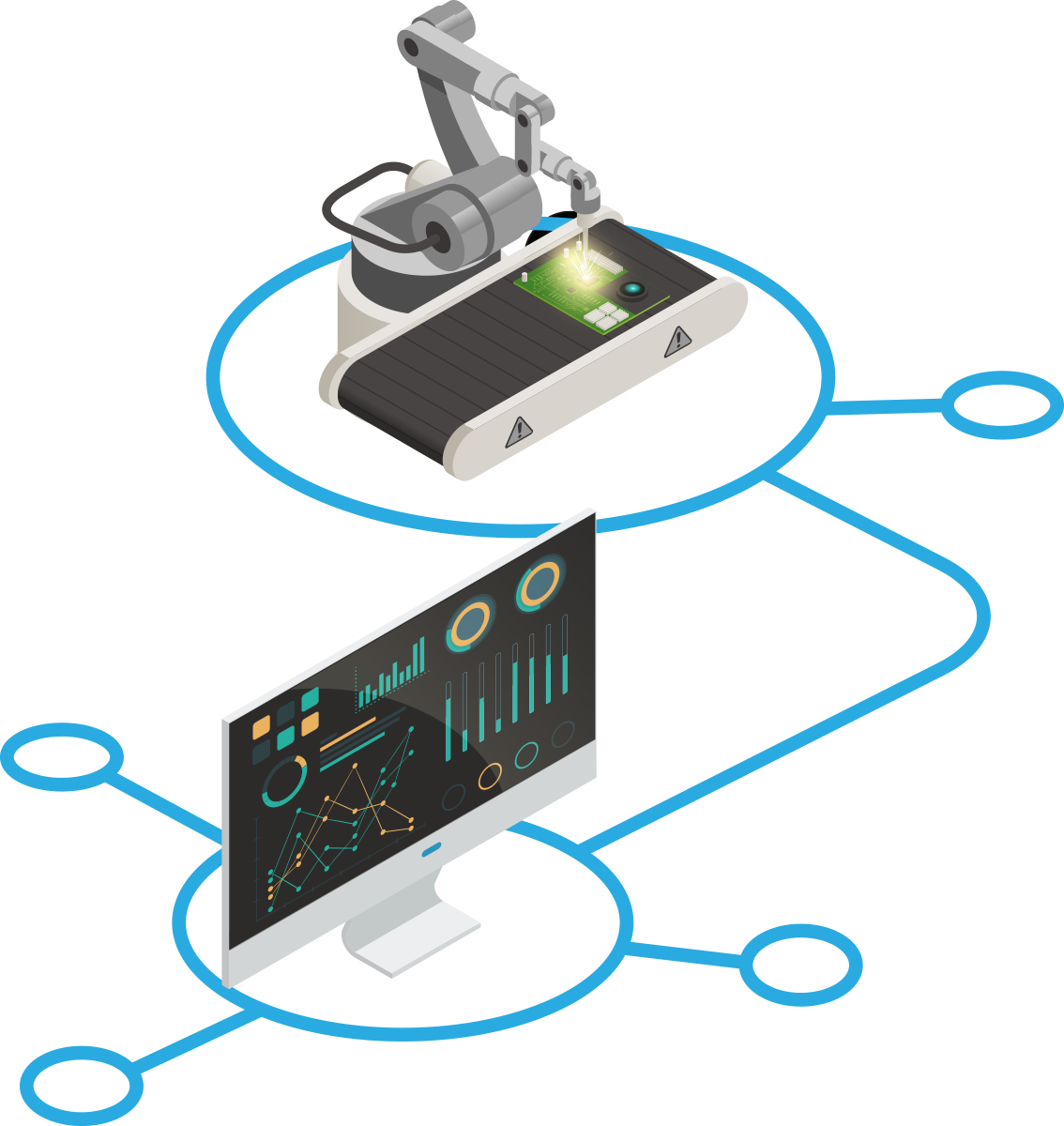